3D-Druck: Mit dem richtigen Schliff zum glatten Bauteil
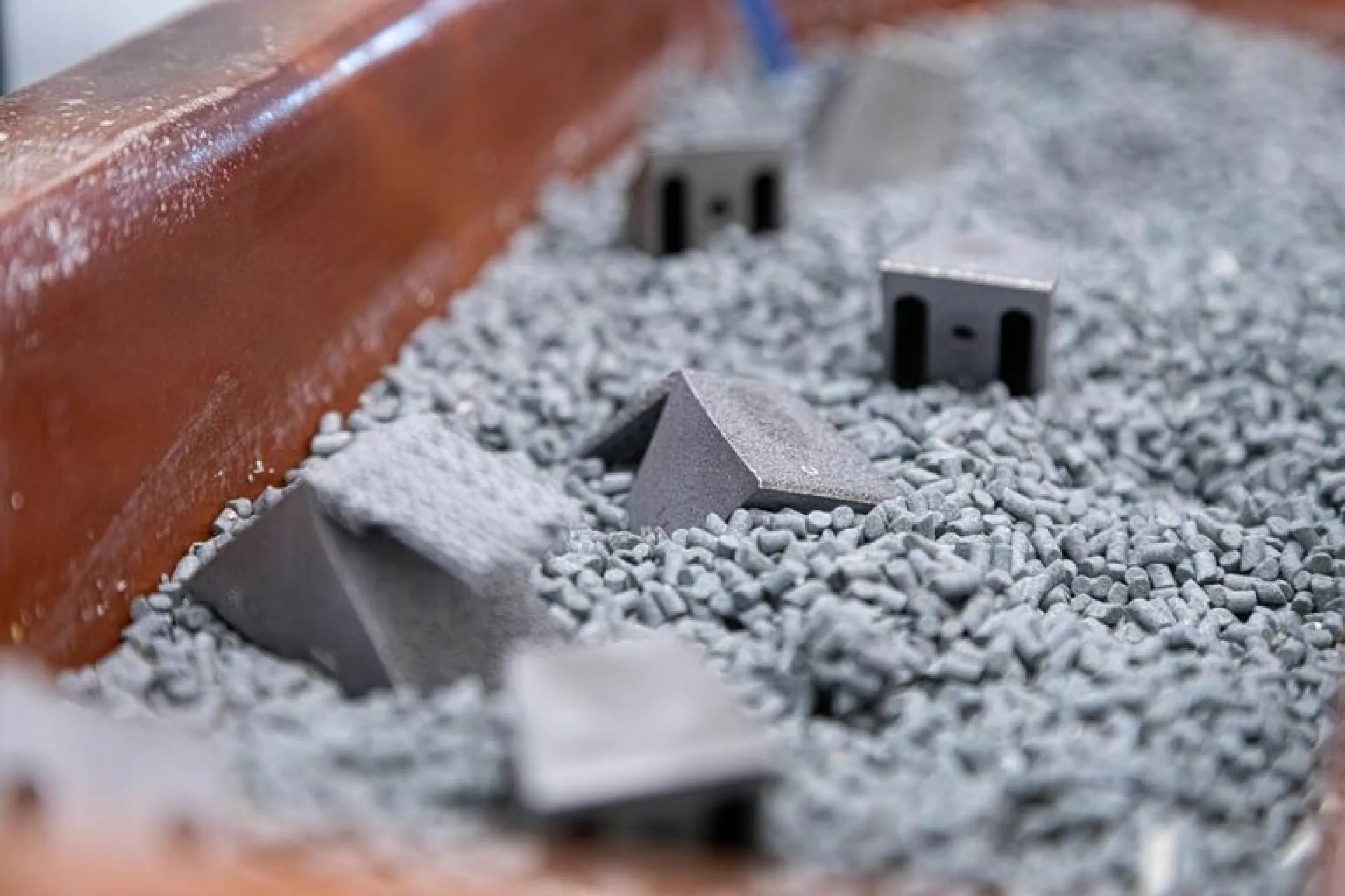
Projekt Clean3D: Automatisierte Anlage die Metall-3D-Druck-Bauteile entpulvert und nachbehandelt
Um ein modulares Maschinenkonzept zu entwickeln, das die automatisierte Entpulverung und Nachbehandlung additiv gefertigter Metall-Bauteile ermöglicht, haben sich das Unternehmen IPS – Innovative Produktionssysteme und das Fraunhofer IPA im Forschungsprojekt „Clean3D“ zusammengeschlossen.
Die additive Fertigung etabliert sich sowohl für Kunststoff- als auch für Metallbauteile immer mehr auch außerhalb von Kleinserien als Fertigungsverfahren in der Industrie. Die Gründe hierfür sind vor allem die Gestaltungsfreiheit, die klassisch spanende oder umformende Fertigung gar nicht ermöglicht, die einfache Skalierbarkeit, die Feingliederung von Strukturen und die bedarfsgerechte Fertigung. Dadurch ergeben sich vielfältige Möglichkeiten und auch Freiheiten in der Bauteil- und Produktionsprozessgestaltung.
Formenvielfalt von Bauteilen erschwert Automatisierung
Dennoch hat der 3D-Druck einige technische Herausforderungen zu überwinden. Darunter fallen vor allem die nachgelagerten Prozesse wie die Entpulverung und die Oberflächennachbearbeitung. Aufgrund der Formenvielfalt der Bauteile und der hohen Variabilität bei Kleinserien sind diese Prozesse oftmals nicht automatisierbar. Die vollständige Prozesskette der additiven Fertigung birgt somit noch Verbesserungspotentiale, um gerade den metallischen 3D-Druck wettbewerbsfähiger zu machen.
Ziel des Projektes „Clean3D“ ist es, eine automatisierte Anlage zu schaffen, die Bauteile vollständig entpulvert und zusätzlich eine hochwertige und gleichbleibende Oberflächengüte für unterschiedliche Bauteile ermöglicht. Innerhalb des Projektes ist das Unternehmen IPS für die Entwicklung der neuen Anlage verantwortlich, während das Fraunhofer Institut für Produktionstechnik und Automatisierung IPA die systematische Testung der möglichen Prozesseinflussfaktoren und die Qualitätssicherung im Prozess übernimmt.
Faktoren für eine hohe Oberflächengüte
In Gesprächen mit mehreren Unternehmen aus der 3D-Druck-Branche erarbeiten die Projekt-Teams die Anforderungen an die beiden Prozesse, um eine anwendungsnahe Vorgehensweise zu gewährleisten. Mit Testbauteilen werden dann die Prozesseinflussfaktoren
- Schleifkörperform,
- Schleifkörperwerkstoff,
- Compound,
- Bewegungsstrategie
identifiziert, um daraus für die untersuchten Werkstoffe eine Lösung zu erarbeiten. Darauf aufbauend werden erste Konzepte für die Anlage entwickelt. In der Zwischenzeit wird ein Konzept zur Prozessüberwachung erarbeitet, in dem unter anderem auch der Verschleiß der Schleifkörper bestimmt wird. Nach Fertigstellung der Anlage wird diese anhand einiger Testbauteile validiert.
Stand des Projekts
Im Oktober 2022 haben die Projekt-Teams bereits einige Gespräche über die Anforderungen der Branche an eine solche Anlage geführt. Sie haben Kernanforderungen gesammelt und die ersten Schritte für das weitere Vorgehen abgeleitet. Darauf aufbauend werden derzeit die ersten Tests an realen Bauteilen durchgeführt, um die Haupteinflussfaktoren auf die Oberflächengüte zu identifizieren. Diese Ergebnisse werden im weiteren Projektverlauf berücksichtigt.
Das Forschungsprojekt „Clean3D“ wird im Rahmen des Förderprogramms „Invest BW“ mit Mitteln des Ministeriums für Wirtschaft, Arbeit und Tourismus Baden-Württemberg (WM BM) gefördert und vom Projektträger VDI/VDE-IT betreut. Das Unternehmen 3D-Laserdruck GmbH & Co.KG, unterstützt das Projekt mit 3D-gedruckten Bauteilen. (eve)