Machines aligned with precision
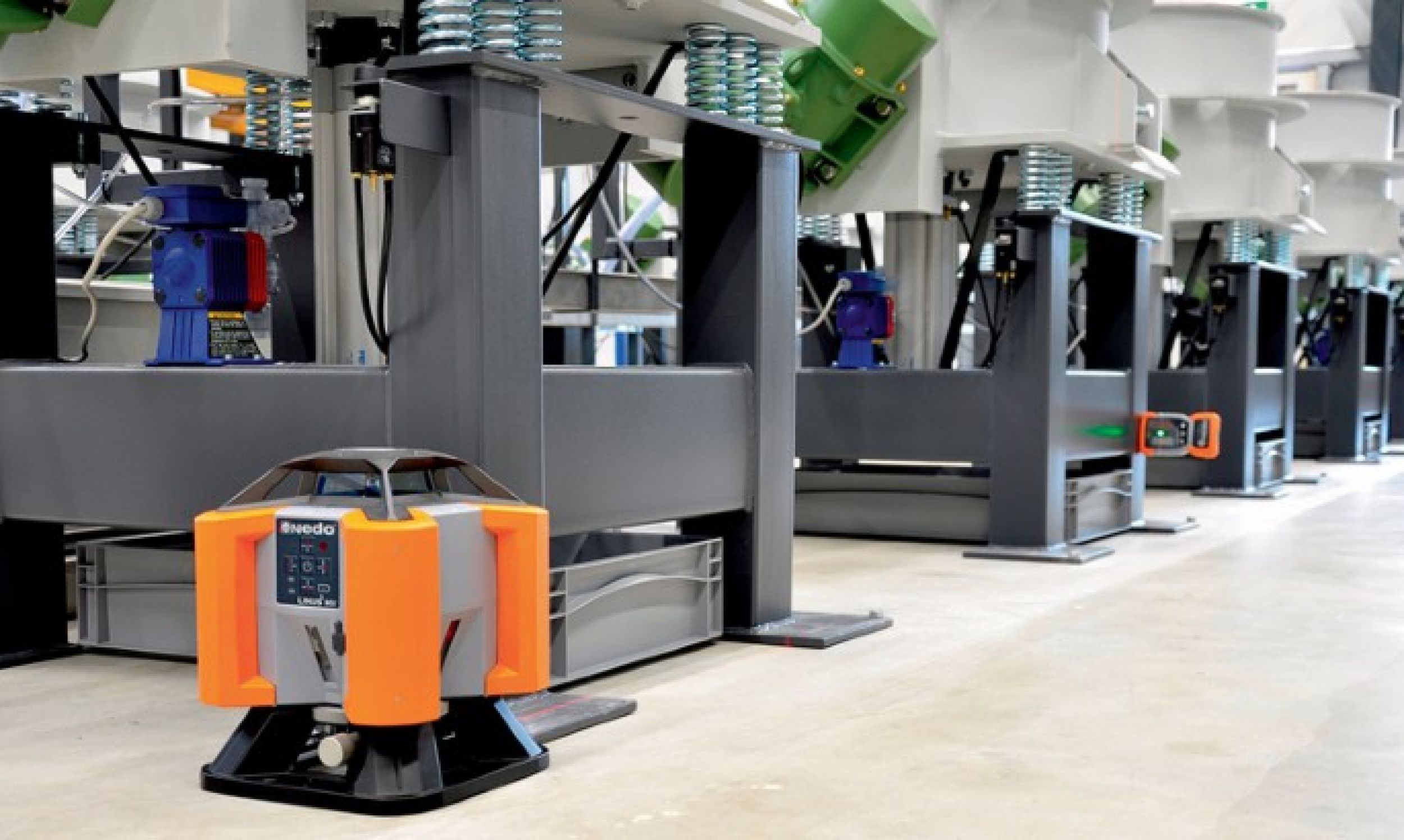
A highly accurate alignment of automation solutions is essential for manufacturing companies to be able to precisely coordinate machines with robots. Therefore, a manufacturer of vibratory finishing systems is using a laser system for the first time to achieve precise and fast alignment of its facility with 24 machines.
The precise alignment of automation solutions is a crucial factor for manufacturing companies, enabling them to accurately coordinate machines with robots and ensure efficient production. Until now, many companies have relied on manual tools such as a string or used theodolites. However, the first method lacks precision, and both approaches require at least two operators. IPS Innovative Produktionssysteme, a manufacturer of vibratory finishing systems, has therefore chosen to use the Nedo Linus 1 HV universal laser system for the alignment of its facility with a total of 24 machines. This allowed the machines to be aligned with a precision of 0.1 mm/m in a quarter of the usual time.
"It took only 30 minutes to align all the machines in the production facility accurately," said Rainer Wälde, Managing Director at IPS, based on his experience. "In the past, such an undertaking would have taken us two hours, four times longer."
Like many engineering companies, IPS previously used a string to arrange its equipment. However, achieving a millimeter-accurate alignment of components was tedious and time-consuming, with an increased risk of errors. The 90° angle arrangement using a right angle based on the 3-4-5 principle also carries the risk of inaccuracy and consumes a lot of time. "We were looking for a solution that is time-saving, precise, and easy to use, and finally decided to use the Nedo universal laser," explained Wälde.
Four vertical laser planes
In addition to a horizontal 360° laser line, the Nedo Linus 1 HV features four individually switchable vertical laser lines, each arranged at a 90° angle to each other. This allows machines to be aligned not only in a straight line but also at specific angles. Downward-facing vertical laser diodes ensure that the laser lines start directly at the base of the device. A plumb beam also marks the intersection point of the four laser lines on the ground, making it easy to align the machines along a single axis.
"One significant advantage of the device is that it can be operated by a single person," added Wälde. The included Nedo Acceptor Line receiver device is equipped with strong magnets and can be easily attached to the machine frame. A digital display with mm resolution shows how far a machine needs to be moved until it is precisely aligned. Bright LEDs, which can be read from a distance, indicate the direction in which the facility needs to be moved.
Horizontal alignment accurate to 0.1 mm/m
In interconnected production processes, the horizontal alignment of individual machine parts to each other plays an important role in enabling smooth transfer of workpieces, for example. At Haug, too, the challenge was to align machines not only in a straight line but also parallel and at a specific height. In the past, leveling instruments were often used for horizontal alignment, but they required two operators. The commonly used frame levels in mechanical engineering are unsuitable despite their high accuracy because they are too short for transferring heights between adjacent machine parts. With the help of the Linus 1 HV's horizontal laser plane, which automatically aligns precisely to 0.1 mm/m, height differences can be quickly detected with the Acceptor Line receiver, allowing for corresponding adjustments.
Long range, easy control
Unlike simple line lasers, the Linus 1 HV can be used for large facilities thanks to its range of up to 80 m. "Our largest facility with 48 machines has dimensions of 60 x 35 m," explained Wälde. "The alignment was significantly simplified using the Nedo universal laser."
Before machines and facility components are bolted to the floor, the Linus 1 HV can also be used for final checks. With the help of the Acceptor Line, the distance to the laser plane can be quickly and easily measured at each machine frame, both vertically and horizontally. The use of the universal laser has reduced the amount of work. Wälde said, "The feedback from our technicians has been positive. We plan to continue using the universal laser for aligning our facilities in the future."//
Contact:
Nedo GmbH & Co. KG
Dornstetten
Tel. +49 7443 24010,
www.nedo.com
Source: JOT 11 | 17